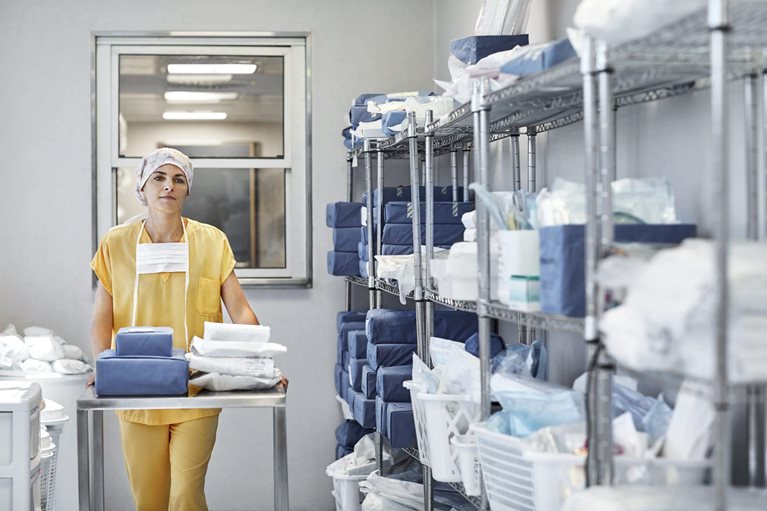
Reducing Hospital Supply Chain Costs While Improving Patient Care
The COVID-19 pandemic has had a severe impact on medical supply chains. Prices increased, some supplies temporarily became unavailable, and some hospitals struggled to quickly get what they need to treat patients.
However, these conditions are just an extreme example of long-existing issues. Hospital supply chain management is historically inefficient, and that's a major problem as the institutions typically run on profit margins under 2%, according to Modern Healthcare. They don't have extra money and cannot prepare themselves adequately for unexpected situations. Health facilities need to better manage their supply chains to ensure the availability of goods when needed while reducing unnecessary costs.
COVID-19 Shows Hospital Supply Chain Cracks
According to NC State University, supply chain management (SCM) is “the active management of supply chain activities to maximize customer value and achieve a sustainable competitive advantage.” So in the case of healthcare, a hospital supply chain is best defined as the process of regularly optimizing medical supply activities to provide patients the best possible care while considering the value of all costs involved.
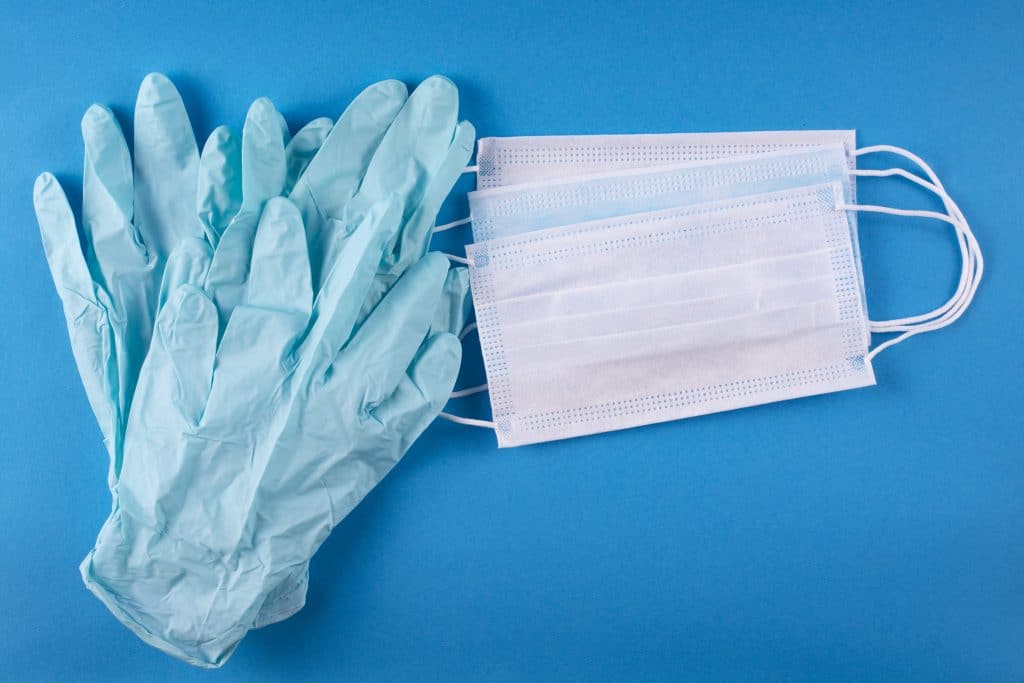
The coronavirus outbreak has stretched healthcare systems almost to the breaking point, and that may partly be because of problems already existing in the healthcare supply chains in the United States. Here are some of the signs during the COVID-19 pandemic that show supply chain weaknesses:
- Healthcare professionals lack the equipment and supplies they need. Ventilators— critical for respiratory failure — are largely unavailable and most hospitals didn't stockpile them. Personal protective equipment (known as PPE) became so scarce, an N95 respiratory mask that cost $1 soared to $6.
- Some common medical equipment and materials became in short supply in large part because China is a major supplier and its own COVID-19 experience disrupted manufacturing.
- Prices in general shot up, which isn't good when 15% of the typical hospital goes to hospital equipment and medical supplies. In some healthcare facilities, like surgery-intensive hospitals, that number can rise to 40%.
The issue of obtaining and distributing supplies, equipment, and drugs has become so serious that hospitals and states well into the pandemic fight said they still have difficulty obtaining the vital supplies they need to combat the outbreak.
Existing Hospital Supply Chain Problems
Facilities are overly reliant on manufacturers in China, creating a single point of supply chain failure. As China dealt with the burgeoning pandemic, its factories closed and the country is the single largest supplier of many medical products. Hospitals depended on supply chains that largely had stemmed from one location.
A study of 2,127 hospitals found that purchasing efficiency in the top quarter of performers concludes that on average, the healthcare industry unnecessarily spends $25.7 billion a year on their supply chain — $12.1 million per hospital.
Supply chain efficiency happens when an organization can standardize their choices, diversify sources of products, and then push for better costs, allowing market competition to help control costs.
Healthcare systems fail to take some foundational steps that can drive efficiency. They need to identify which services, products, and procedures are necessary, according to clinical evidence. Institutions also need to use data to limit practitioners' preferences for materials and equipment, and find options that provide similar performance at a lower cost.
Here are three ways health facilities can approach supply chain improvement while reducing costs and increasing patient care:
1) Rethink Your Strategy
To solve supply chain issues, hospitals need to step back from their usual practices and reconsider their strategy. Advance planning for emergencies should become routine, even if the need is sporadic. Administrators and executives can begin to steer their organizations to better practices of maintaining inventory supply. And teams of professionals from clinical scheduling and practice, procurement, and operations can collectively manage insight over different areas of responsibility and information.
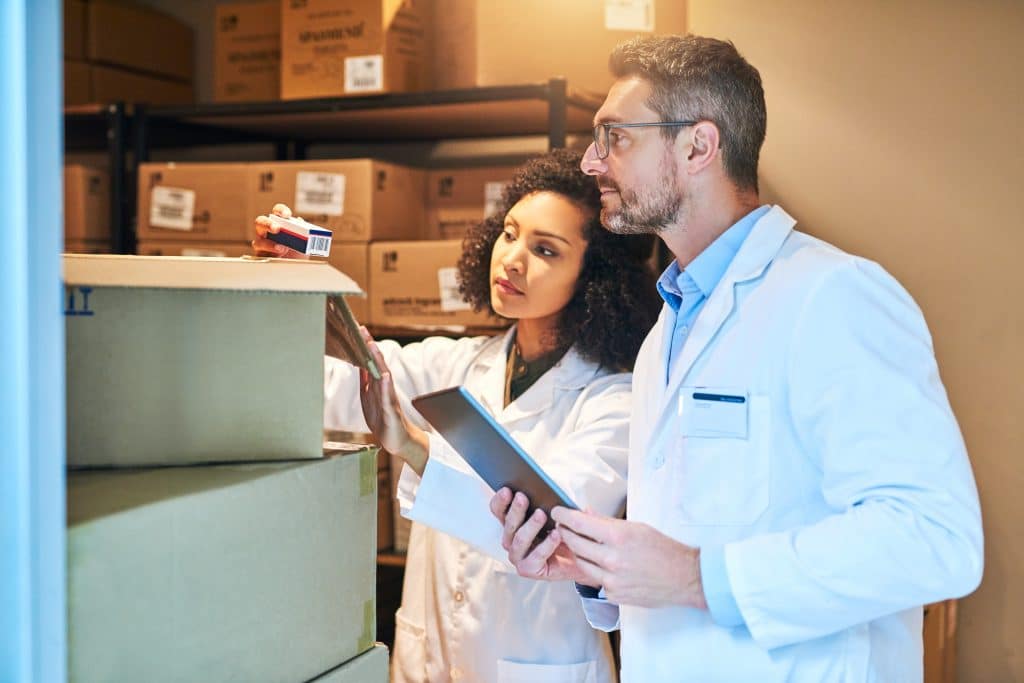
An hour outside of Boston is a warehouse that holds boxes labeled "pandemic product" for the day that Massachusetts General Hospital needs the PPE and IV fluid the pandemic might require. The hospital had started examining its supplies and anticipating what might happen because of dependence on China as a source. As of the time of the report time in March, the hospital had been holding off tapping the supply but expected, as case loads increased, that the warehouse contents would help them get through "the worst two weeks," as Dr. Paul Biddinger, chief of emergency preparedness at Mass General, put it.
Hospitals might also consider two separate sets of supplies: one for normal needs and another for surges in demand, whether due to pandemics or natural disasters, each with its own stocking strategy and storage. With enough money saved on supply chain purchases, it can become possible to have and store multiple sets of inventory, off-site if necessary, such as at a PODS storage center. With space mass medical supply storage, hospitals can prepare for surges or even place larger order volumes of inventory for better costs.
2) Technology Can Help
The University of Kentucky Chandler Hospital has turned a basement space into a supply chain "war room" for its COVID-19 response. A long table holds computers and notepads, and papers cover the walls as personnel try to track the complex interactions of local and global supply chain demand.
As organized as the effort mentioned above seems, technology is able to make this more efficient. Real-time supply chain management systems using advanced technology can track inventory and forecast demand before it happens. Radio-frequency identification (RFID) and Internet of Things (IoT) devices can help a healthcare facility track equipment over wireless connections and better manage receiving shipments and handling quality issues and returns.
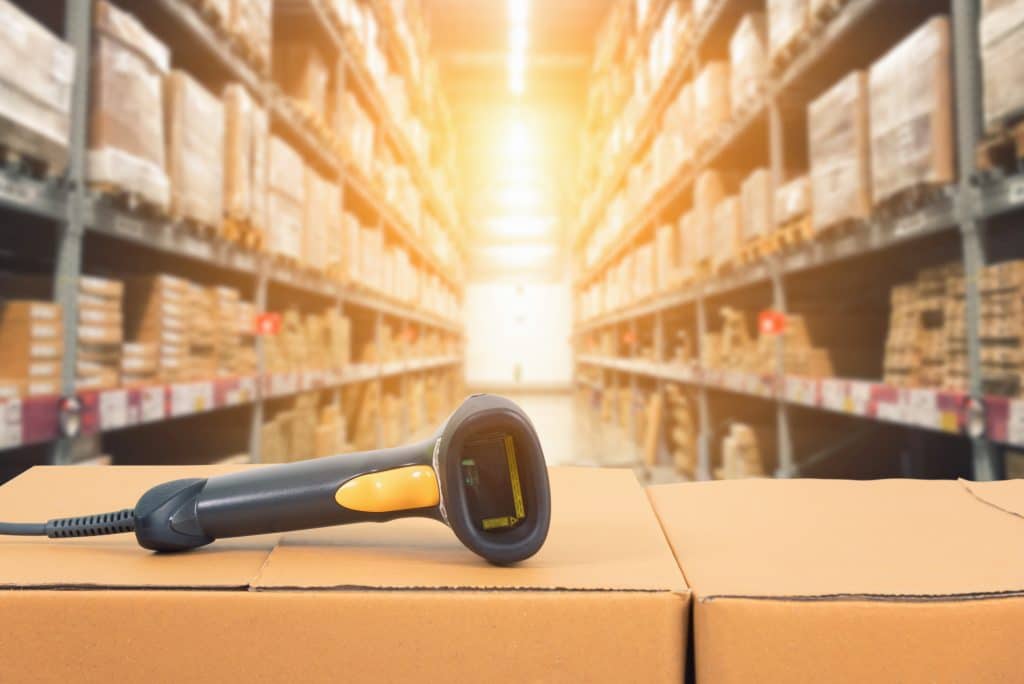
Hospital systems can start by having better visibility into what they have and need. A healthcare system can create digital control towers — virtual decision centers that track the locations of materials, supplies, and equipment at all times. For a hospital, that means having immediate insight into what equipment and supplies are on hand, what might be free when needed, when items are equivalent and potential substitutes, and if additional purchases are necessary.
3) Flexible Storage Solutions
One lesson the coronavirus pandemic teaches is the need for flexible storage. A hospital should have the space available for emergency supplies -- and even medical office storage when facilities need to make room inside for more patient care areas during emergencies. Facilities may also have to set up secure medical supply storage containers at improvised alternative care facilities to accommodate surges patients needing attention.
PODS portable containers are a useful tool for streamlining hospital supply chains. As they improve their supply chains and save money, hospitals can invest in mass quantities of medical inventory far in advance. These medical supplies can be kept inside containers at a PODS secure storage facility, and hospitals can have those containers delivered by PODS when and where needed to cover transportation supply chain demands. The strategy helps better manage supply chain logistics avoiding shortages and the high prices that come in their wake.
Learn more about how hospitals can create more space for medical supplies and equipment through PODS portable healthcare storage solutions.
[maxbutton id="3"]
Comments
Leave a Comment
Your email address will not be published. Required fields are marked *