
How to Minimize Last-Mile Delivery Inefficiencies
Last-mile delivery may be the most visible piece of the supply chain, yet the least understood.
It might look like delivery of paper products to the office down the street or restaurant supplies to the local pizza shop. And in the age of widespread e-commerce, it looks like Amazon holiday gift deliveries on your neighbor’s front porch.
In short, last-mile deliveries are the final movement of product from a distribution center to the customer.
At best, companies struggle to make the final leg of the supply chain cost-efficient. At worst, the final mile becomes the straw that breaks an end-to-end delivery budget. That's why it's no surprise that last mile can comprise as much as 53 percent of overall shipping costs.
The age-old problem of last-mile delivery has confounded logistics management for years. But that doesn’t mean there aren’t solutions for making the most of this crucial piece of the puzzle.
What Is Last-Mile Delivery?
Every supply chain has a last mile, whether it’s a business-to-business (B2B) supply chain or a business-to-consumer (B2C) supply chain — or sometimes both.
Last-mile delivery can casually be defined as the last leg of a product's journey, which is typically from a distribution point or transportation hub to the consumer or end destination.
Let's go back to that example of the paper supplies company at the beginning of this article. Its customers can include anything from a big-city office building to a retail partner, to a suburban home. This variety of destinations in the delivery process can make routing the last mile difficult.
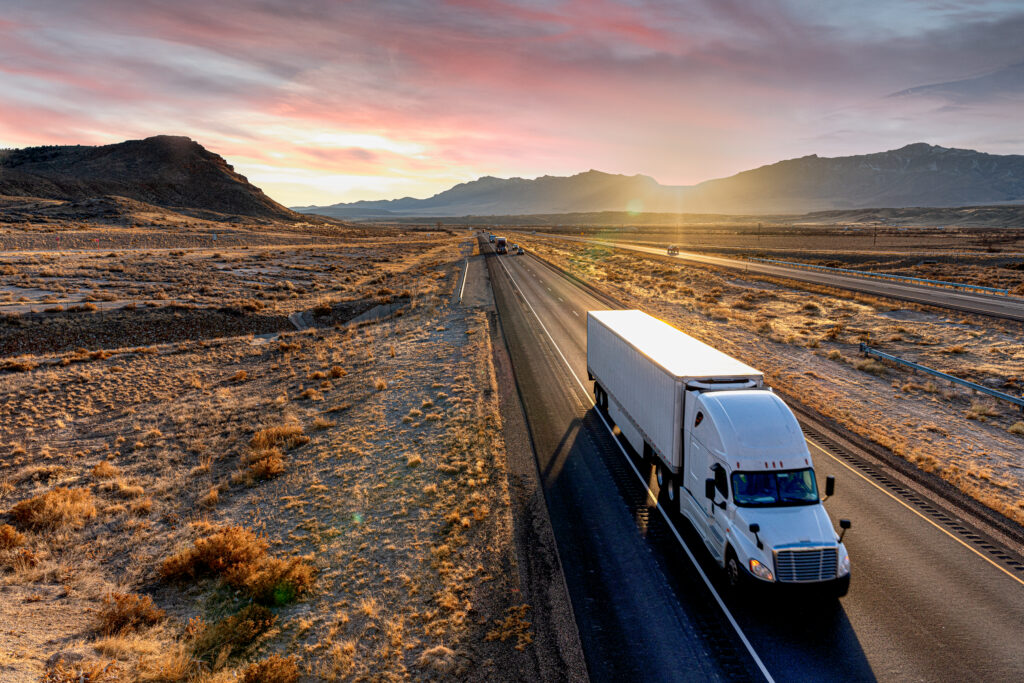
The types of trucks involved in last-mile delivery vary as well. While they are often parceled service trucks, like UPS or FedEx, they sometimes involve LTL freight carriers in the case of suburban or rural delivery points.
The LTL process can also involve an additional layer of partnering with warehousing and delivery providers.
In other words, last-mile delivery can look very different from one company to the next, and from one end customer to the next. There is no one-size-fits-all recipe for this highly visible yet complex process for the last stage of shipping.
What Makes Last Mile So Challenging?
Because of the wide variety of routes, endpoints, and trucks involved, the last mile is often a company’s biggest headache.
From congestion navigating within big cities to having multiple drop-offs in various towns or rural areas, the last mile is the toughest mile to solve.
Increased order fulfillment demand during the pandemic only added to the volume of complexities experienced in last-mile delivery. While certain businesses in the past might have only served the typical city or suburban business, that all changed due to COVID.

The same concept applies to e-commerce. The COVID-19 pandemic rapidly accelerated the already growing e-commerce stream.
Instead of going out to the store, for instance, consumers pivoted to wanting home delivery of nearly every item on their lists, ranging from groceries and clothing to exercise equipment and construction supplies.
These challenges increase costs at all parts of the shipping process. Fuel for trucks, lost time spent idling in traffic, or simply the great amount of time spent getting from one stop to the next all adds up.
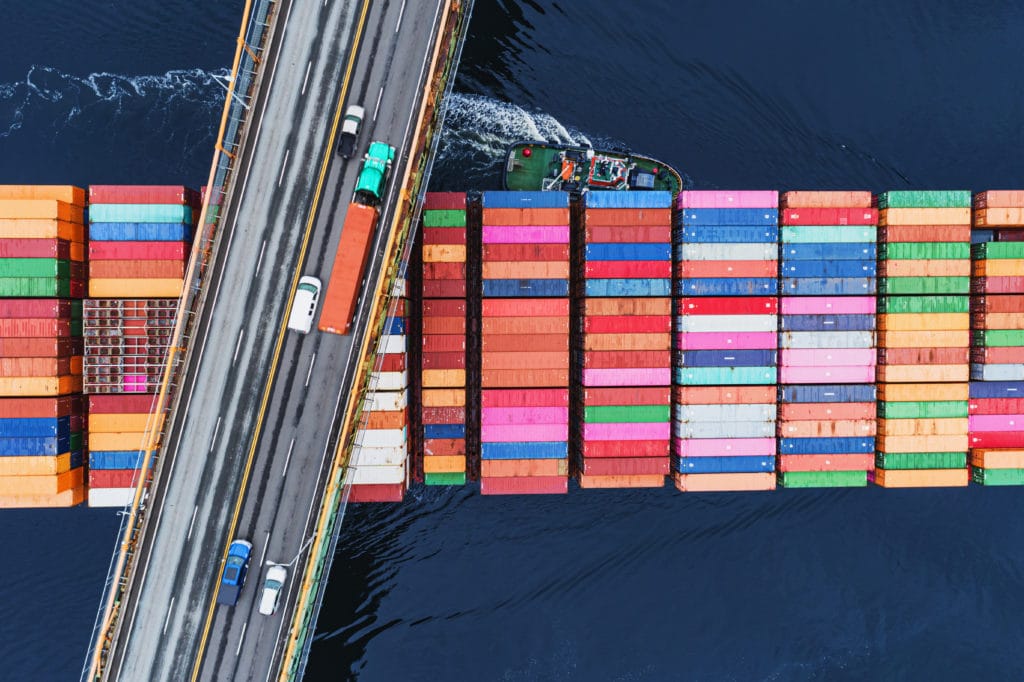
Companies may also not have distribution centers located close enough to delivery points or may lack a sufficient number of distribution centers to make that final mile anywhere close to efficient.
In addition, many distribution centers are located in industrial hubs rather than in areas in close proximity to end customers, such as a city or a suburb.
How Can You Overcome Last-Mile Challenges?
Partnering with providers, such as PODS for Business, can play a big role in removing last-mile inefficiencies. With dedicated support to streamline last-mile processes, you can even turn your company's logistics into a competitive advantage.
The combinations of ways PODS can solve your last-mile delivery challenges are nearly endless. When it comes to this final piece of the puzzle, decreasing the complexity and increasing the efficiency is what you are after, PODS can help you reach that goal.
Take, for example, the scenario mentioned earlier in this article about how distribution centers are often far from endpoint customers. PODS containers can bridge that gap by because they can serve as mini warehouse spaces closer to your customers.
Businesses can simply place PODS containers in strategic locations where they can house and pull deliveries efficiently so they arrive to the customer faster and more efficiently.
Have large-scale deliveries to make? The PODS nationwide network can transport entire container loads to your customer. Upon destination arrival, PODS can once again serve as storage if needed, solving additional end-customer challenges in the mix.
If you’re seeking a solution to your own last-mile delivery challenges, take a look at how PODS Logistics & Supply Chain Solutions can help.
[maxbutton id="1"]
RELATED ARTICLE: LTL Shipping: Best Practices to Follow When Using LTL & Freight Carriers
Comments
Leave a Comment
Your email address will not be published. Required fields are marked *